HSW SERIES SPOT WELDER PRODUCT COMPARISON
|
Junction condition depends a lot on the metal types and the electrodes, and also on the plunge pressure of the electrodes. All comparison tables and data do not guarantee that the model concerned can weld as well as mentioned. Please use this as reference only.
|
|
HSW- 01A |
HSW- 02A |
��Stainless Steel Wire
Diameter in mm |
Stainless Steel Wire (Diameter in mm) |
Stainless Steel Wire
Diameter mm |
|
0.5 |
0.9 |
1.2 |
1.6 |
0.5 |
AA |
AA |
AA |
AA |
0.9 |
|
AA |
AA |
A |
1.2 |
|
|
A |
B |
1.6 |
|
|
|
B |
*) Using stick electrode; the 1.6 mm ones are pre-processed. |
��Stainless Steel Wire
Diameter in mm |
Stainless Steel Wire (Diameter in mm) |
Stainless Steel Wire
Diameter mm |
|
0.5 |
0.9 |
1.2 |
1.6 |
0.5 |
AA |
AA |
AA |
AA |
0.9 |
|
AA |
AA |
AA |
1.2 |
|
|
AA |
AA |
1.6 |
|
|
|
A |
*) Using stick electrode; the 1.6 mm ones are pre-processed. |
��Stainless Steel Plate
|
Stainless Steel Plate (Thickness in mm) |
Stainless Steel Plate
(Thickness in mm) |
|
0.1 |
0.3 |
0.5 |
0.1 |
AA |
|
|
0.3 |
|
|
|
0.5 |
|
|
|
*) Using HSW-W2 ��Picture on strength evaluation |
��Stainless Steel Plate
|
Stainless Steel Plate (Thickness in mm) |
Stainless Steel Plate
( mm) |
|
0.1 |
0.3 |
0.5 |
1.0 |
0.1 |
AA |
AA |
AA |
|
0.3 |
|
AA |
AA |
|
0.5 |
|
|
|
A |
1.0 |
|
|
|
B |
*) Using HSW-W2 Picture on strength evaluation |
Stainless Mesh
|
Diameter (mm) / line / cm |
Diameter
(mm)
/ line / cm |
|
0.15/13 |
|
0.15/13 |
|
|
|
|
|
|
|
|
*) More of the test result will be printed out soon.. |
��Stainless Mesh
|
Diameter (mm) / line / cm |
Diameter
(mm)
/ line / cm |
|
0.15/13 |
|
0.15/13 |
AA |
|
|
|
|
|
|
|
|
|
LEGEND
AA |
The junction strength needed for practical things is mechanically and electrically acquired. |
A |
It is mechanically jointed, but the junction strength is weaker compared to AA. |
B |
It is electrically jointed, but there is a possibility of breaking down. Additional fixation would make it usable. |
C |
Cannot be jointed. It will break if it falls from 1 m height. |
|
Steel Plate (Iron (SS ESK)
Thickness in mm |
|
SK 0.4 |
SK 0.5 |
SS Steel 0.23 |
B |
|
|
SK Steel 0.4 |
|
C |
|
SK Steel 0.5 |
|
|
C |
Stainless steel 0.1 |
A |
|
|
*) Are still being tested. |
Steel Plate (Iron) (SS ESK)
Thickness in mm |
|
SK 0.2 |
SK 0.3 |
SK 0.4 |
SK 0.5 |
SS Steel 0.23 |
AA |
|
|
|
|
SK Steel 0.2 |
|
AA |
|
|
|
SK Steel 0.3 |
|
|
AA |
|
|
SK Steel 0.4 |
|
|
|
AA |
|
SK Steel 0.5 |
|
|
|
|
A |
|
|
Welding Different Metals To
S50C, SS400, SKD11 Blocks
Type / Thick (mm) |
Steel Block (16x60x60mm) |
|
|
|
|
|
|
|
|
|
|
|
|
|
|
Copper Plate
0.2mm |
C |
Copper Wire
0.2mm |
AA |
|
|
|
��Plating Steel Plate
(Thickness mm) |
|
Zync 0.3 |
Tin 0.15 |
|
|
Zync 0.3 |
|
C |
*) Are still being tested. |
�� Plating Steel Plate
(Thickness mm) |
|
Zync 0.3 |
Tin 0.15 |
AA |
|
Zync 0.3 |
|
C |
Tin:heavy steel plate Zinc:galvanized steel plate |
|
Aluminum Foil
Type / Thick mm |
Al Foil μm |
Al Foil 100μm |
Al Foil 220μm |
Aluminum Foil μm |
AA |
|
|
Aluminum Foil 100μm |
|
AA |
|
Aluminum Foil 220μm |
|
|
A |
|
HSW- 01A |
HSW- 02A |
��Thermocouple
Diameter mm |
|
Note |
Chromel - Alumel center diameter 0.32 mm |
AA |
Power Controller HSW-PC1 was used |
Copper - Constantan center diameter 0.32 mm |
AA |
Power Controller HSW-PC1 was used |
Copper - Constantan center diameter 0.1 mm |
AA |
Power Controller HSW-PC1 was used |
*) Power Controller HSW-PC1
and welding pinset HSW-W2 were used.
Copper - Constantant 0.1 mm Pictures (2007.10.30) |
��ThermocoupleNew
Diameter in mm |
0.32 |
0.1 |
0.1/
0.025 |
Chromel - Alumel |
AA |
AA |
AA |
Copper - Constantan |
AA |
AA |
|
For 0.32mm welding, Power Controller HSW-PC1 and
stick electrode were used.
Other than 0.32mm, Power Controller HSW-PC1 and
thermocouple pinset HSW-TC1 were used.
|
��Battery and Nickel Plate
Battery / Lead |
Nickel Plate |
Copper Wire (mm) |
|
HSW-N12 |
HSW-N25 |
HSW-N64 |
0.18 |
0.3 |
0.5 |
CR2032
|
B |
|
|
AA |
C |
C |
CR2025
SONY |
AA |
|
|
|
|
|
LR44
|
AA |
|
|
AA |
B |
C |
LR41
|
AA |
|
|
AA |
AA |
C |
ene-Loop
SANYO |
A |
|
|
|
|
|
GP2500
(GP A) |
AA |
|
|
|
|
|
HR-4/3FAU
SANYO |
AA |
|
|
|
|
|
CP-2400
SANYO |
AA |
|
|
|
|
|
|
��Battery and Nickel Plate
Battery / Lead |
Nickel Plate |
Copper Wire (mm) |
|
HSW-N12 |
HSW-N25 |
HSW-N64 |
0.18 |
0.3 |
0.5 |
CR2032
|
AA |
AA |
|
AA |
AA |
AA |
CR2025
(SONY) |
AA |
AA |
|
|
|
|
LR44
(GP) |
AA |
AA |
|
AA |
AA |
AA |
LR41
(GP) |
AA |
AA |
|
AA |
AA |
AA |
ene-Loop
SANYO
P3 |
AA |
AA |
AA |
|
|
|
GP2500
(GP A) |
AA |
AA |
AA |
|
|
|
HR-4/3FAU
SANYO |
AA |
AA |
AA |
|
|
|
CP-2400
SANYO |
AA |
AA |
AA |
|
|
|
|
The measures of Nickel Plate used in the table above :
Model |
Thickness |
Width |
HSW-N12 |
0.08 mm |
3.2 mm |
HSW-N25 |
0.15 mm |
3.2 mm |
HSW-N64 |
0.15 mm |
6.4 mm |
|
LEGEND
AA |
The junction strength needed for practical things is mechanically and electrically acquired. |
AA�� |
Additional undercut on the nickel plates is needed to achieve the same result as AA. |
A |
It is mechanically jointed, but the junction strength is weaker compared to AA. |
B |
It is electrically jointed, but there is a possibility of breaking down. |
C |
Cannot be jointed. |
|
|
�� Battery and Phosphor Bronze Plate
Phosphor Bronze Plate |
0.15 mm |
0.2 mm |
Alkaline A Battery |
AA |
A |
Alkaline AA Battery |
AA |
|
��Strength Evaluation Pictures
|
�� Battery and Stainless Steel Plate |
�� Battery and Stainless Steel Plate |
Stainless Steel Plate |
0.1 mm |
0.2 mm |
LR44 (GP) |
AA |
|
|
|
|
|
Stainless Steel Plate |
0.1 mm |
0.2 mm |
LR44 (GP) |
AA |
AA |
|
|
|
|
HSW- 01A |
HSW- 02A |
|
�� Platinum and Brass Wire
Wire Type / Diameter mm |
Platinum Wire 0.3 mm |
Note |
Platinum Wire 0.3 mm |
AA |
Power Controller HSW-PC1 was used. |
Wire Type / Diameter mm |
Brass Wire 0.5 mm |
Note |
Brass Wire 0.5 mm |
AA |
Power Controller HSW-PC1 was used. |
|
|
��Copper and Stainless Plate
Plate Type / Diameter mm |
Stainless Plate 0.1 mm |
Note |
Copper Plate
0.15mm |
A |
Stick Electrode HSW-EB1 and HSW-PC1 were used. |
|
|
�� Different Kind of Metals
Type / Diameter mm |
Stainless Steel
0.2 mm |
Brass
0.2 mm |
Bronze
0.15 mm |
Nickel
0.15 mm |
AA |
AA*1 |
AA*3 |
Nickel
0.08mm |
AA
|
AA*1 |
AA*3 |
Stainless Steel
0.2 mm |
|
AA*2
|
A |
Plate Type / Diameter mm |
Stainless Plate 0.1 mm |
Note |
Copper Plate
0.15 mm |
A |
*4 |
Stick Electrode HSW-EB1 was used.
[ Welding Electrodes and Piling Order ]
*1) Stick Electrode - Nickel - Brass - Welding Pen
*2) Stick Electrode - Stainless Steel - Brass - Welding Pen
*3) Stick Electrode - Nickel - Copper - Welding Pen
*4) Stick Electrode - Stainless Steel - Copper - Welding Pen
|
|
�� Welding different kind of metals to
S50C, SS400, SKD11 Steel Blocks
Type / Thickness mm |
Steel Block (16x60x60mm) |
|
|
|
|
|
|
|
|
|
|
|
|
|
|
Copper Plate
0.2 mm |
C |
Copper Plate
0.2 mm |
AA |
|
|
*) The strength of the junctions above are not evaluated. |
HSW- 01A |
HSW- 02A |
|
|
Spot-Welded Junction's Tensile Strength Evaluation
|
[ ABOUT THE EXPERIMENT AND HOW TO READ THE DATA ]
This experiment is conducted in order to know how strong is mechanically a welding junction welded with HSW Series. The strength value of a welding junction is affected by a lot of factors, so please use this as reference only.
The test pieces (experiment materials) are shown in the right picture. At the welding junction on the right, the right L-shaped part will be fixed using a vise. On the left side of the test piece, loops will be made and will be fixed with spot welding. The loop part, since it is a part to hang the hook of the spring balance for measurements, it will be different from the evaluated part; forces other than the ones on the shear direction will also work. Using the same load the test was done three times, and only if the results were the same for at least two times will the results be posted here.
Based on these strength evaluation results, the AAABC value of the product comparison on the upper half of this page is decided.
AA means enough strength mechanically; for junction between metals, it means it can hold more than 20kgf of load. Also, for battery, it means it can hold more than 5kgf.
A means about half of AA in strength. It is not sufficient, but even at this level it is usable for some purposes.
B means it will not break down if it falls from about 2m height to a concrete floor, and it cannot hold more than 3kgf. It still can be used for temporary fixation such as soldering, and also for parts that need temporarily electrical connectivity and do not being applied to external forces.
C means it will be joint temporarily, and it will break down if it falls from about 2m height to a concrete floor. |
|
|
Stainless Plate (0.3 mm thick) |
Stainless Plate (0.5 mm thick) |
|
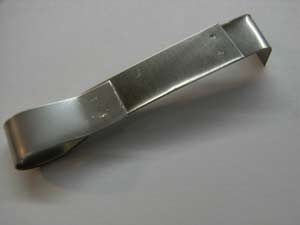 |
[ Experiment Materials ] Stainless Plate 0.3 mm thick 10mm wide
[ Machine Used ] HSW-01A and HSW-W2
a maximum 25 kg of a spring balance
[ Welding Method ] pile up 5 mm and weld in 4 points
[ Power Settings ] Standard Power Supply
|
[ Experiment Materials ] Stainless Plate 0.5 mm thick 10mm wide
[ Machine Used ] HSW-02A and HSW-W2
a maximum 25 kg of a spring balance
[ Welding Method ] pile up 5 mm and weld in 2 points
[ Power Settings ] Standard Power Supply with maximum pulse width |
[ RESULT ]
|
LOAD |
APPLIED TIME |
CONDITION |
1 |
5 kgf |
30 mins |
no change (continued to 2) |
2 |
10 kgf |
60 mins |
no change |
3 |
12 kgf |
12 hours |
no unusual conditions up to 20kg |
|
The front and the back of the test piece's welded section.
|
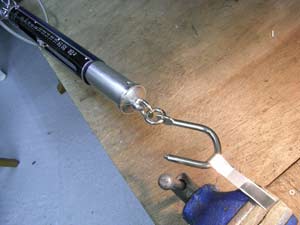 |
[ RESULT ]
|
LOAD |
APPLIED TIME |
CONDITION |
1 |
7 kgf |
30 mins |
no change (continued to 2) |
2 |
14 kgf |
30 mins |
no change (continued to 3) |
3 |
20 kgf |
6 hours |
no unusual conditions |
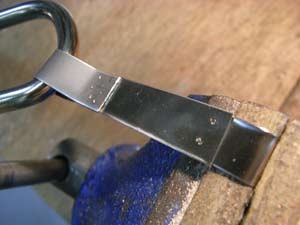
|
|
|
|
|
|
HSW-02 (PREVIOUS MODEL OF 02A) |
Stainless Steel Plate (0.5 mm thick) |
Battery and Nickel Plate (shear direction) |
|
|
[ [Experiment Date ] October 29th, 2007
[ Machine Used ] HSW-01A + HSW-W2
[ Experiment Materials ] SUS 0.5mm - SUS 0.5mm in thickness
[ Result ]
|
LOAD |
APPLIED TIME |
CONDITION |
1 |
5 kgf |
90 mins |
no change (continued) |
2 |
8 kgf |
|
break off |
|
[ REQUIREMENTS ] Weld unto C size NiCad battery�fs negative electrode a HSW-N25 (width 3.2mm x 0.15 thick nickel plate) using the welding pen (included in the standard pack), and afterwards weld a stainless line 0.9mm in diameter unto the nickel plate in three points, which will be the test piece. (Click the picture to zoom in) |
|
[ Measurement ] The load is hung on the shear direction of the spot junction using a normal spring balance. |
Stainless Plate (0.5 and 0.1 mm in thickness) |
|
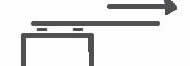
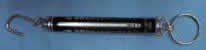 |
[ [Experiment Date ] October 29th, 2007
[ Machine Used ] HSW-01A + HSW-W2
[ Experiment Materials ] SUS 0.5mm - SUS 0.1mm in thickness are piled up and welded in two points
[ Result ]
|
LOAD |
APPLIED TIME |
CONDITION |
1 |
10 kgf |
180 mins |
no change (continued) |
2 |
20 kgf |
4 hours |
no unusual conditions |
|
|
|
[ Result 1 ] The junction can hold 7 kgf for 5 minutes, and there are no unusual conditions in the junction part. |
|
|
|
[ Result 2 ] After holding 7 kgf for 5 minutes, the weight is slowly increased, and at 9 kgf the spot junction between the battery and nickel plate broke down. |
|
|
|
[ Result 3 ] Look at the nickel plate after breaking down. There was a trace of spot junction. (Click the picture to zoom in) There are no unusual conditions in the three points of stainless line and the stainless loop line. |
|
[ Machine Used ]
(1) HSW-02 and welding pen (included in standard pack)
�i(2) 25 kgf tensiometer
[ Test Materials ]
(1) HSW-N25 �iwitdh3.2C0.15mm thick of Nickel plate�j
(2) Diameter 0.9mm of stainless line |
|
|
|
HSW- 02A |
|
Nickel Plates (shear direction) |
|
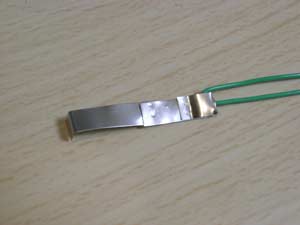
Nickel plates 0.15mm in thickness are piled up and welded in two points
no unusual condition after adding up 10 kg for 10 minutes (at the middle part)
(the part connected to the tensionmeter shows a sign of breaking up)
[Machine Used ]
(1) HSW-02A and welding pinset (HSW-W2)
(2) 25 kgf tensiometer
[ Test Materials ]
(1) HSW-N64 �iwidth 6.4 x 0.15 mm thick of Nickel Plate) |
HSW- 01A |
|
Phospor Bronze (0.2 mm in thickness) |
Phospor Bronze Plate (0.2 mm in thickness) |
|
|
[ Experiment Date ] November 4th, 2007
[ Machine Used ] HSW-01A and welding pinset (HSW-W2)
[ Experiment Materials ] Phosphor bronze 0.2mm in thickness welded in two points
[ Result ] (1) 8 kgf 60 mins OK
(2) broke up after adding up more than 10 kgf |
[ Experiment Date ] October 29th, 2007
[ Machine Used ] HSW-02A and welding pen (included in standard pack)
[ Experiment Materials ] Phosphor bronze 0.2mm in thickness and A battery's negative electrode
[ Result ] (1) 5 kgf 90 mins OK
(2) broke up after adding up more than 8 kgf |
|
Steel Plate (SS Plate 0.23mm in thickness) |
|
|
|
[ Experiment Date ] November 4th, 2007
[ Machine Used ] HSW-02A and welding pinset (HSW-W2)
[ Experiment Materials ] SK Steel 0.23 mm in thickness is piled up with 5 mm and welded in two points
[ Result ] (1) 10 kgf 90 mins OK
(2) 20 kgf 120 mins no unusual conditions |
|
Steel Plate SK Steel 0.5mm in thickness |
|
[ Experiment Date ] November 4th, 2007
[ Machine Used ] HSW-02A and welding pinset (HSW-W2)
[ Experiment Materials ] SK Steel 0.4 mm in thickness is piled up with 10 mm and welded in two points
[ Result ] (1) 10 kgf 90 mins OK
(2) 20 kgf 120 mins no unusual conditions |
|
[ Experiment Date ] November 4th, 2007
[ Machine Used ] HSW-02A and welding pinset (HSW-W2)
[ Experiment Materials ] SK Steel 0.5 mm in thickness is piled up with 10 mm and welded in two points
[ Result ] (1) 10 kgf 90 mins OK
(2) 20 kgf 90 mins no unusual conditions |
HSW- 01A |
HSW- 02A |